April 12, 2018
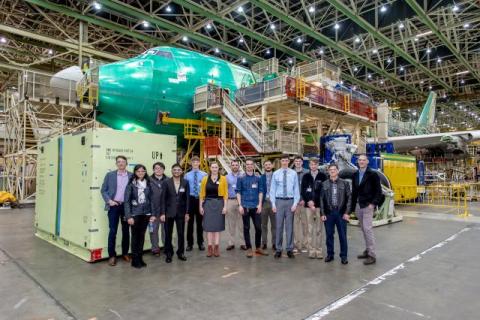
Collaborative robotics, haptic alert systems for hearing-impaired employees and riveting safety. These are just a few of the projects University of Washington students from the Boeing Advanced Research Center (BARC) showcased at the Future of Flight Museum during a recent meeting with Boeing engineering leadership. University of Washington STEM students from the Boeing Advanced Research Center toured the Boeing Everett Factory after presenting their research projects to Boeing engineering leadership. (Photo from Boeing Communications.)
“We want students to gain hands-on experience in the BARC and come work for Boeing to build the greatest airplanes in the world,” said Todd Zarfos, Boeing Commercial Airplanes (BCA) Engineering leader and Boeing focal for the University of Washington, during the kick-off of the event.
The group of undergraduate and graduate students span multiple UW Engineering Departments and presented on the technologies they’re developing in the lab with the guidance of Boeing senior managers like Blaine Felton and lab manager Kevin Bray, among others. Bray, a Materials & Manufacturing Technology (MMT) engineer and team lead for the BARC, works on campus with the students providing guidance on their ongoing projects throughout the year. Project engineers from BCA Product Development, BR&T MMT and Manufacturing Technology Integration (MTI) and Environment Health and Safety (EHS) meet students and faculty weekly to advise and assist on project strategy and implementation.
This year’s group of students focused on collaborative robotics, mechanic-assisting technology, riveting safety improvement and additive manufacturing processes, among other advanced manufacturing solutions.
Parker Owan, a University of Washington graduate student, shared how his Mechanic Assistance Collaborative Tool (MASCOT) could help mechanics perform assembly tasks in enclosed spaces more safely: “Using collaborative robots for remote or hazardous manufacturing applications could help ensure mechanics’ health and safety in the production environment, especially when visual access is limited.”
The solutions developed in the BARC are designed to one day transition from the lab to the factory. Amy May, director of Boeing Workplace Safety, said, “This type of work needs to happen and will help Boeing team members build our products as safely as possible.”
In 2017 Boeing hired its first full time BARC alumni. Six BARC students have been hired as 2018 Boeing summer interns and will be working in BR&T and BCA Product Strategy and Future Airplane Development.
Above writeup adapted from article by Janelle Bernales, Boeing Communications