Transforming titanium with 3D printing
“Titanium 3D printing has the potential to open new pathways in additive manufacturing for industries ranging from health to aerospace,” says ME professor Ramulu Mamidala, who leads the Metal 3D Printing Lab as part of the Washington state-funded JCDREAM (Joint Center for Deployment and Research in Earth Abundant Materials) initiative. “It’s really about discovering the art of the possible.” In 2017, UW acquired a 3D printer capable of printing titanium. It’s the only one of its kind at the UW and one of just a few at universities across the country. For additional information and on how to collaborate read the article by Chelsea Yates
Bill Kuykendall (left), Professor Ramulu Mamidala (center) and Research Scientist Rishi Pahuja (ME PhD ’19)
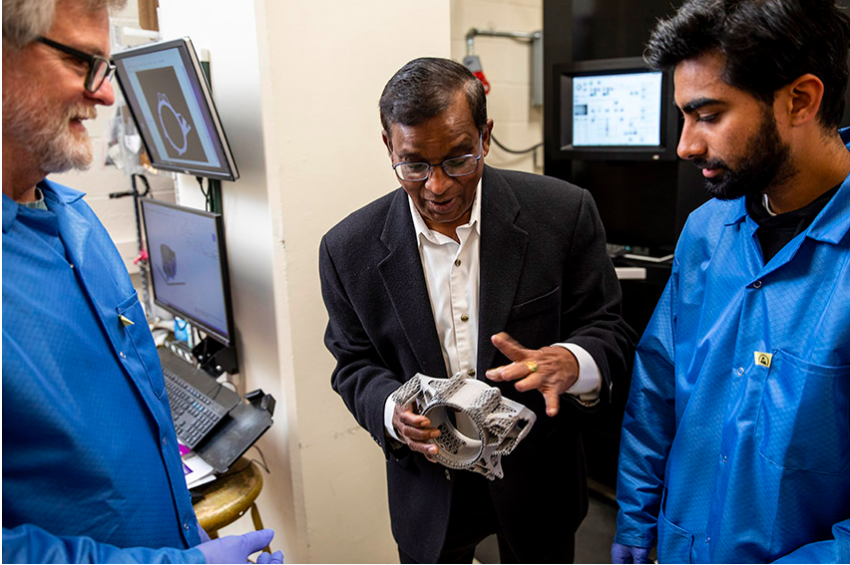
Additive Manufactured Metal Crush Cartridge Lattice Structures
When a plane takes off from the runway, the tail end of the airplane occasionally collides with the runway. To minimize damage to the body of the airplane, the aircrafts are equipped with a tail skid device that is responsible for absorbing the impact energy from the contact. The tail skid device is composed of a series of pins, links, and a crush cartridge, which is a hydraulic cylinder containing a honeycomb lattice structure that is allowed to crush under a load. This is the part of the device responsible for absorbing the impact energy. These parts behave similar to the “Crumple Zone” in a car, except the crush cartridge limits damage solely to the cartridge and is replaceable. The problem with the current crush cartridge is it is very expensive and time consuming to manufacture. Therefore, it is beneficial to develop a lattice structure that can perform to the same standard as the current crush cartridge but is also capable of being additively manufactured with minimal post processing.
Example of a Lattice Structure
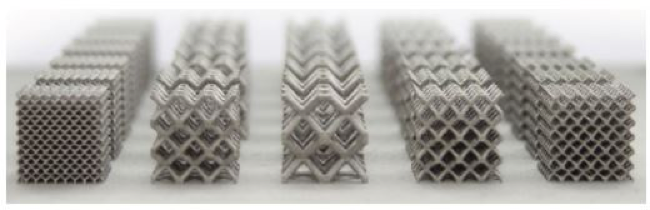
Background
A lattice structure is defined as a connected network of struts. The purpose of a lattice structure is to create a strong, stiff, load carrying structure that requires less material than a traditional solid structure. Previously, lattice structures were very difficult to manufacture due to their complex geometry; however, with the advent of additive manufacturing, it has become relatively easy to manufacture almost any type of lattice structure and in a shorter amount of time. The design freedom of additive manufacturing has allowed the creation of complex lattice structures to enhance part performance. The ability of lattice structure to effectively use material is especially attractive in industries where the benefits of weight reduction are significant. There are several factors that influence the behavior of lattice structures, outlined in the figure below, with the most important (arguably) being the geometry of the unit cell, which governs how the structs respond to a load, as well as determining if it is a bending dominant or tension dominant structure. For the application of crush cartridges, bending dominant structures are preferred.
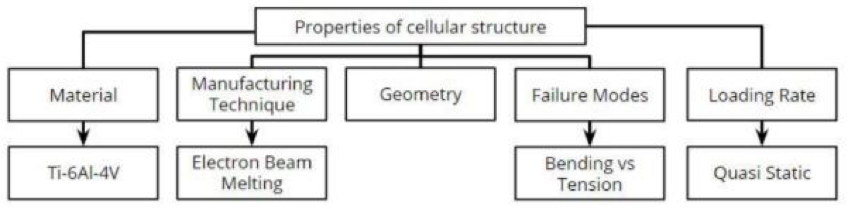
Method and Analysis
Based on analytical methods, octahedral and pyramidal unit cells of lattice structures were seen to be the most promising and efforts are focused on those type lattices. The structures were iteratively modeled and 3D printed, optimized, and then tested in a compression test. The tests provided stress-strain curves that were compared to ideal curves to derive an energy absorption efficiency. When analyzing the compression test videos, it was observed that failure occurred at the nodes of the lattices. This was especially true at the at the nodes connected to the base plate. Overall, pyramidal lattices had the best performance with regard to energy absorption, absorbing 79% of its ideal curve energy. However, because a crush cartridge would consist of a highly scaled structure that would not be affected so severely by boundary conditions it is still not perfectly clear that a pyramidal structure with no boundary conditions would be the best choice for the application.
Optimal Pyramidal Lattice Structure
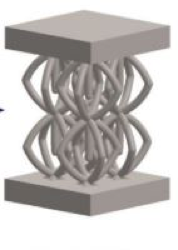
Researchers Involved
Mamidala Ramulu, Dwyane Arola, Ashis Banerjee, Corie Cobb, Junlan Wang, Stefanie Meier, and Andrew Baker