At the BARC, students work with Boeing engineers and faculty to find ways to make airplane assembly and manufacturing more efficient, intelligent, automated, and streamlined. Example areas include machine learning, 3D printing, designing lift devices, and robot control interfaces. Please see some examples below and tap into individual project links for more details.
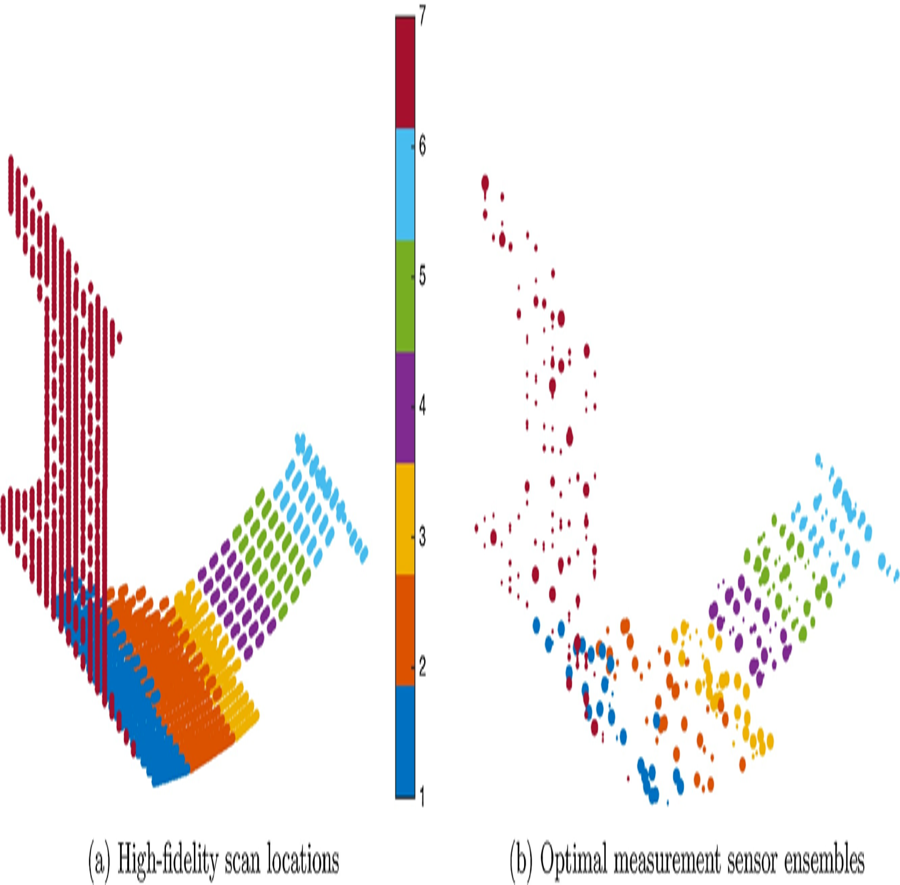
Advanced manufacturing is increasingly a data-rich endeavor, with big data analytics addressing critical challenges in high-tolerance assembly, operation planning, quality control, and supply chains. At the BARC, we are collaborating with experts at Boeing to capitalize on their wealth of data for many high-priority applications in aircraft manufacturing.
Multi-Robot Collaboration
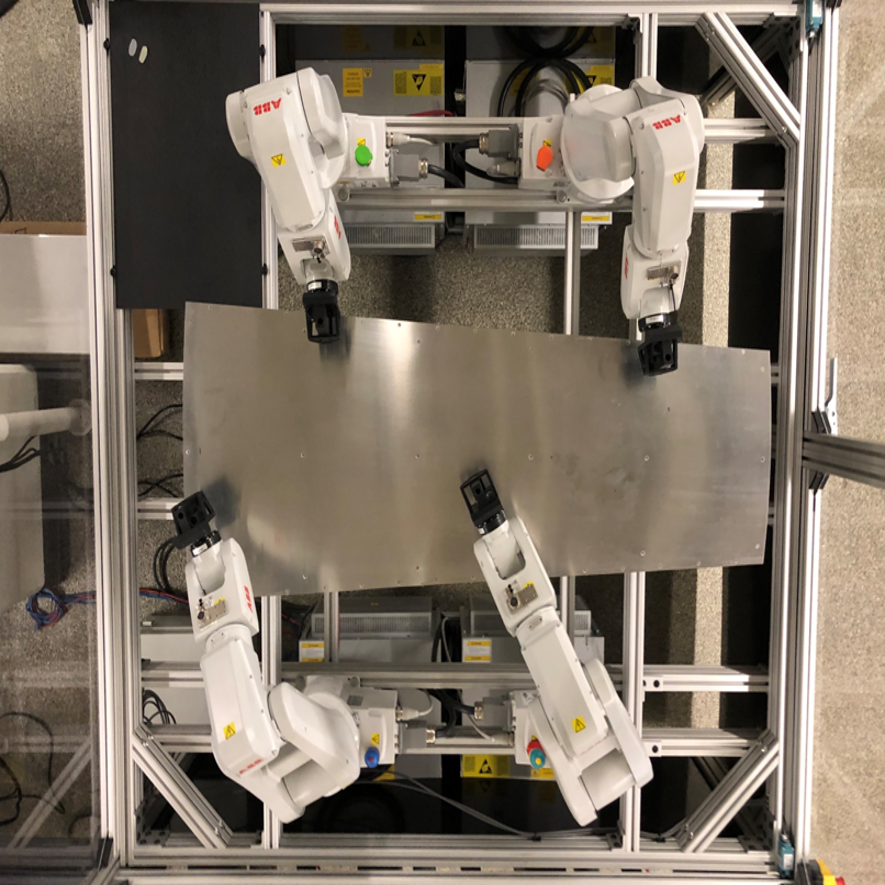
Efficient utilization of cooperating robots in the assembly of aircraft structures relies on balancing the workload of the robots and ensuring collision-free scheduling.
Additive Manufacturing
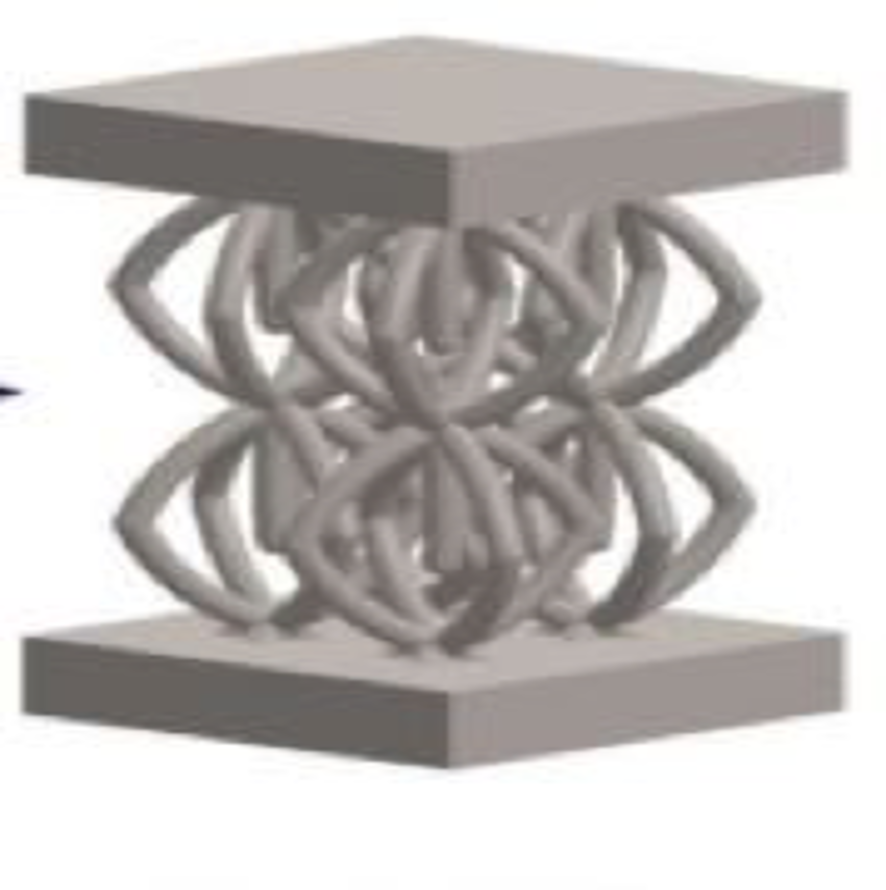
UW acquired a 3D printer capable of printing titanium. It’s the only one of its kind at the UW and one of just a few at universities across the country. It has been used to design various projects, including the design and fabrication of crush cartridges used in airplane tails to absorb the impact energy transferred during a potential tail skid. In the event of a tail skid, crush cartridges can reduce costly body damage during landing. This project sought to understand and quantify the efficiency of various additively manufactured lattice structures in absorbing impact energy.
Sanding Assist System
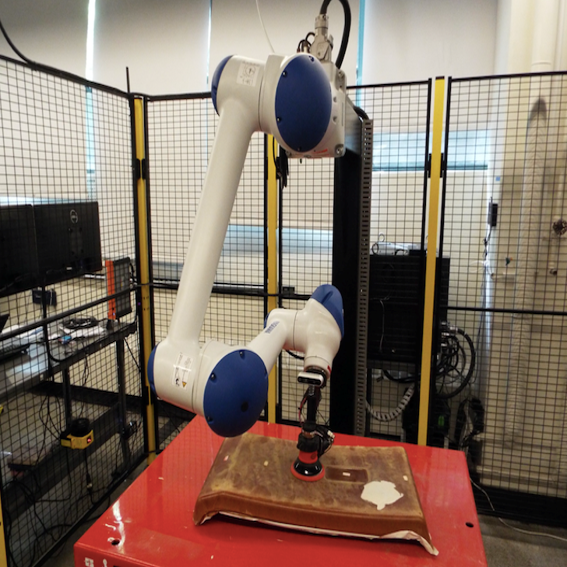
Sanding is often performed using an air-powered, hand-held random orbit sander. The vibration transmitted to the hand of the operator is an ergonomic risk that needs to be mitigated.
Gesture Selection for Human Robot Interaction
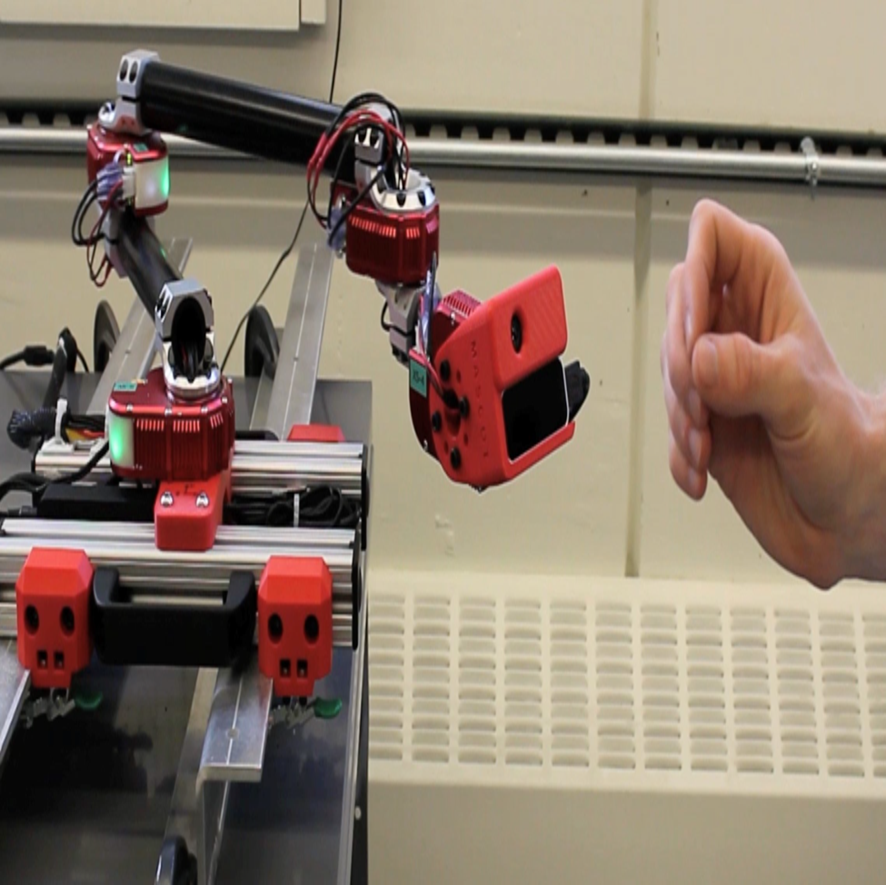
During manufacturing operations in limited-access areas, such as an airplane wing, mechanics can often reach into the working space with a single hand but cannot see it due to the tight space configuration. The resulting work is slow and can be imprecise. An appropriately placed camera that can be controlled with hand gestures made by a mechanic can provide significant benefits to the efficiency and quality of the work.
End Effector Control
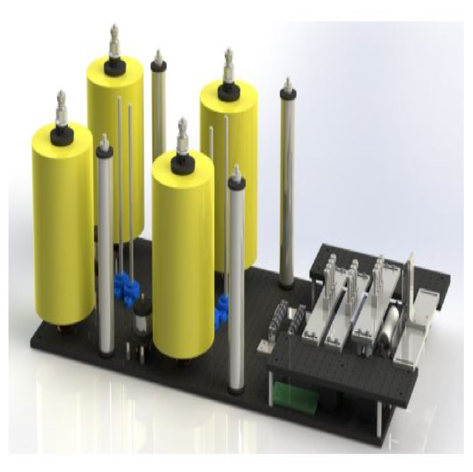
The BARC End Effector project looks to improve process efficiency and performance while applying composite material onto a surface using a robotic arm paired with a separately controlled end effector.
Limited Access Manufacturing
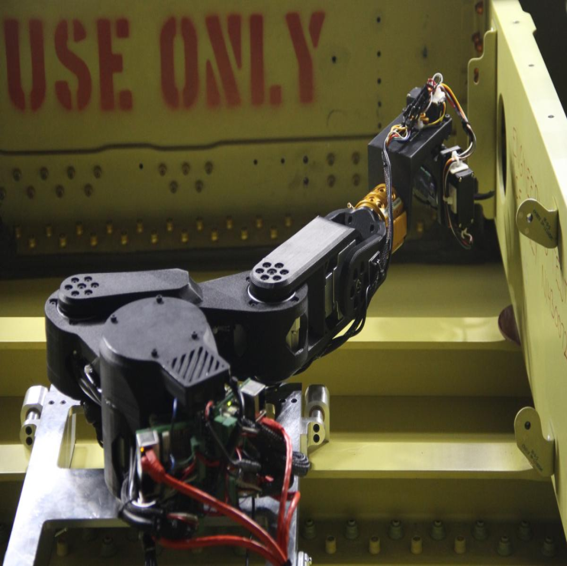
Manufacturing tasks in confined spaces (such as a wingbox) present challenges that include i) severely restricted allowable configurations, ii) mapping of and localizing to partially-known environments, and iii) robust perception for tracking features and regions of interest.
Human-Machine Collaborative Robotics
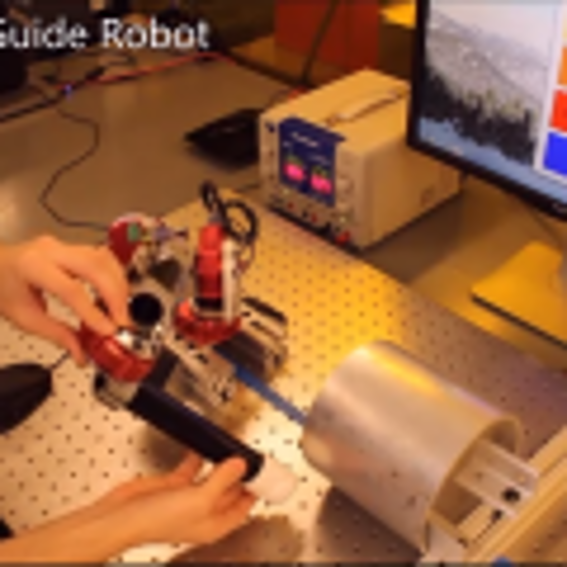
Collaborative robotics in manufacturing can provide mechanics with intelligent and multi-functional tools to improve mechanic health and safety while increasing work efficiency.